
More than 24 per cent of industrial fires in the world are caused by electrical faults. The East African region has in past few years experienced an upsurge of petroleum storage and vending facilities, manufacturing plants and industrial facilities. It has been noted that most of these do not conform to the laid down regulations and international best practice on construction. This is especially in electrical design, which is critical in preventing danger of electrocution, fire or explosions.
To ensure safety, it is essential that petroleum vending equipment and facilities are correctly planned, designed, installed, tested and commissioned as articulated in different rules, regulations, legislation and guidance from international best practice. There after, regular periodic inspection and testing are required to ensure that these facilities are safe. Poorly designed or installedor badly maintained electrical facilities have presented significant risks of shock, fire or explosion caused by ignition sources such as sparks, overheating, lightning, or electro magnetism.
The region has several spirits and paints manufacturing plants, LPG plants, and petroleum storage plants among others – all of which are prone to the mentioned risks. The Electrical Safety Audits (ESA) performed on explosive environment, oil and gas drilling rigs, and industrial facilities revealed risks of explosions in such facilities.
Among the Electrical Safety Audited facilities, effects of diverted neutral currents, lack of hazardous areas classification, high loop impedance, high earth resistivity, elevated equipment temperature, overloads, poorly designed systems, and compromised insulation resistance, were some of the causes of fire and explosion.
The regulators in East Africa have mandates on regulation of transmission, distribution, and consumption of electrical and petroleum energy among others. Enforcement of mandatory periodic Electrical Safety Audits (ESA) by all energy regulators in East Africa to international standards and best practice to secure the facility from fires and explosions is key. This will contribute considerably to the investors in the region getting their return on investment – courtesy of safe facilities.
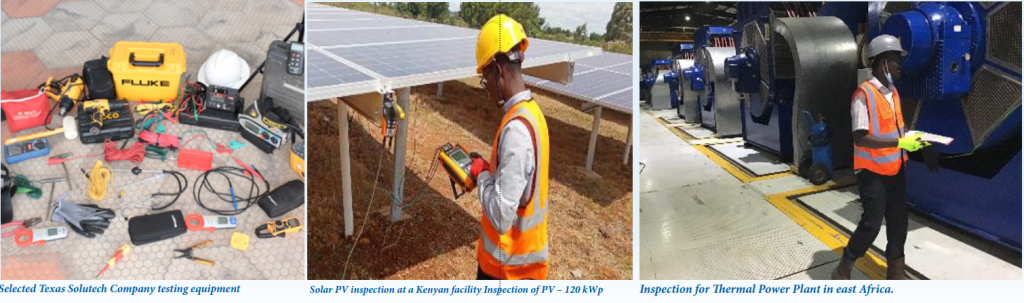
Comprehensive guidance addresses good practice in the planning, design, installation, testing, and commissioning of electrical installations at industrial and petroleum product stations. This is about both new and refurbished, including electrical supplies, and cabling for pump systems, leak prevention or detection, tank gauging, closed circuit television (CCTV) and computer systems.IEC standards, Electricity at work regulations (EWR), Dangerous Substances and Explosive Atmospheres Regulations 2002 (DSEAR), Red Guide, Blue Guide and other British standards have rich regulations if followed. They are likely to support longer-lasting investment in the region free from fires and explosions. The guidance is intended to assist electrical competent persons to provide, maintain or verify electrical installations, petroleum storage equipment, and vending facilities. The outcome should provide an effective electrical installation and give site operators and owners confidence to claim compliance to international standards and best practice.
Texas Solutech Co. Ltd has invented a point-based software for Electrical Safety Audits (ESA).
Article by: Texas Solutech Company. The company has certified engineers by regulator Energy and Petroleum Authority of Kenya (EPRA) and Engineers Board of Kenya(EBK). It has undertaken more than 1000No. ESA in Eastern Africa.